Comparison of Thermal Insulation Properties
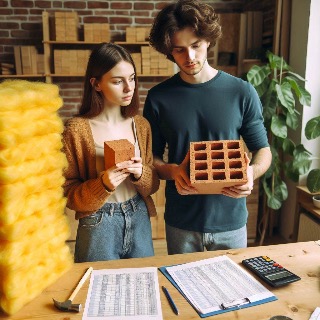
Whenever we talk about the price-value ratio of a building, it is important to understand the underlying aspects of the property. This includes the material and construction date of the load-bearing structure, the condition and design of the foundation, the structural and aesthetic state of the ceiling and roof structure, and, if there is an upper floor or extension, whether its design and condition are adequate.
Whenever we talk about the cost-value ratio of a building, it is important to interpret the underlying content of the property.
That is, what materials were used and when the load-bearing structure was built, the condition and design of the foundation, the condition of the ceiling and roof structure both statically and aesthetically, and whether there is a mezzanine or extension, whether its design and condition are adequate. But it is also worth examining the structures with discerning attention, not just calculating square meter prices. There can be significant differences in terms of energy performance between modular, prefabricated, or monolithic structures, as it's important to mention that the transportability (size limits), craneability (weight limits), and design of walls and interior spaces in mobile and modular houses are influenced by road transport regulations. Before comparing the numbers, it is advisable to clarify a few terms and legal regulations that are essential parts of the design and construction process.
The ÉTDR (Construction Documentation and Information System) is a Hungarian online platform that manages the building permit and notification procedures. The TNM regulation refers to the 7/2006 (V. 24.) TNM regulation, which defines the energy performance requirements for buildings.
1./ How does the ÉTDR work with the TNM regulation?
The ÉTDR is used for managing building permits and notifications, and the submitted documents may include energy performance calculations and certificates related to the building, which are prepared based on the requirements outlined in the TNM regulation.
2./What energy performance requirements must be met?
The 7/2006 (V. 24.) TNM regulation specifies the minimum energy performance requirements for new and existing buildings. These requirements can be met on the following three levels:
- Heat transfer coefficient (U-values) of the structures
Regulates the thermal insulation of the building's individual structural elements (walls, roof, windows, etc.).
For example, the maximum U-value for facade walls can be 0.24 W/m²K.
The glazing U-value can be up to 1.0 W/m²K.
The maximum U-value for the lower ceiling must be 0.26 W/m²K.
The U-value for a ground-floor slab can be 0.30 W/m²K.
The maximum U-value for a heated attic roof and flat roof is 0.17 W/m²K.
- Total energy performance characteristic (Ep-value)
Determines the building's primary energy consumption in kWh/m²/year.
New buildings must be nearly zero energy buildings (BB rating) after June 30, 2022.
- Renewable energy share
At least 25% of the building's energy consumption must be covered by renewable sources if it is a new building.
3./ When must energy performance compliance be verified?
- For new buildings: Compliance must be verified in the design phase.
- For existing buildings undergoing renovation: If significant modifications are made, the building must meet the prescribed energy performance requirements.
- Before occupancy: An energy certificate verifies the building's actual energy efficiency.
4./ How does the process work in the ÉTDR?
- Design phase
The architect/energy expert prepares the thermal calculations and the energy compliance documentation.
The documentation is submitted through the ÉTDR system for permitting or notification.
- Construction process
During construction, it must be ensured that the materials and technologies used comply with the TNM regulation's requirements.
- Occupancy procedure
The building's energy certificate must be submitted for the occupancy permit.
The relevant authority reviews the submitted documentation in the ÉTDR.
The subject of the review is the comparison of prefabricated, masonry, or monolithic structures with given structural layers. It is important to mention that none of these technologies are inherently better or worse than others in terms of their function. The provided source and the U-value calculator used for the review and comparison may not be 100% precise, as professionals certified for issuing energy certificates perform calculations in a more accurate manner, but the tool can give us an approximate value. It is also important to note that the heat transfer calculator does not interpret thin layers, such as technological, vapor barrier, windproof, or moisture-permeable foils. These elements play an essential role in the functionality of walls but are typically not considered significant in terms of thermal insulation. It should also be noted that the online insulation calculation program works with whole centimeters, and the rounding and structural thicknesses are determined accordingly.
5./ Wall Structures and Their Energy Performance
Wall Structure 1: 44 cm thick masonry wall with 10 cm facade insulation and 2 cm of plaster on both sides. The wall's U-value = 0.23 W/m²K, which meets the regulation.
Wall Structure 2: 15 cm thick EPS sandwich panel wall, with windproof foil on the outside, a ventilated wooden cladding of 3 cm, and a vapor barrier foil on the inside, finished with 1 cm thick plasterboard. The wall's U-value = 0.22 W/m²K, which meets the regulation.
6./ Ground-floor Slab Structures and Their Energy Performance
Wall Structure 3: 25 cm thick monolithic concrete foundation wall, with 15 cm of XPS thermal insulation on the outside and 2 cm of DRYVIT plaster, and 2 cm of plaster on the inside. The wall's U-value = 0.215 W/m²K, which meets the regulation.
Wall Structure 4: 10 cm thick EPS sandwich panel wall, with windproof foil on the outside, a ventilated wooden frame with 3 cm, and a construction board cladding of 1 cm, along with a vapor barrier foil and 1 cm thick battens on the inside. The wall's U-value = 0.31 W/m²K, which does not meet the regulation.
7./ Attic and Roof Structures and Their Energy Performance
Ground-floor Slab Structure 1: Prefabricated structure with PVC floor covering (1 cm), MgO board (2 cm), PUR foam insulation (5 cm), XPS thermal insulation (5 cm), and monolithic concrete slab (10 cm). The structure's U-value = 0.192 W/m²K, which meets the regulation.
Ground-floor Slab Structure 2: Tile covering with adhesive bed (2 cm), concrete slab (5 cm), technology foil, XPS thermal insulation (10 cm), protective separation layer + waterproofing, monolithic concrete slab (10 cm), crushed stone filling (10 cm). The structure's U-value = 0.23 W/m²K, which meets the regulation.
Unheated Attic Floor Structure 1: OSB board (2 cm), vapor-permeable foil, 15 cm of glass wool insulation between beams, vapor barrier foil, and covered wooden board cladding (2 cm). The structure's U-value = 0.17 W/m²K, which meets the regulation.
Unheated Attic Floor Structure 2: Upper metal covering, air gap (3 cm), vapor-permeable foil, 5 cm of glass wool insulation, air gap (2 cm), vapor barrier foil on the lower sheet, batten frame, and air gap (1 cm), OSB board (2 cm), and plasterboard (1 cm). The structure's U-value = 0.236 W/m²K, which does not meet the regulation.
8./ Heated Attic Roof Structure and Their Energy Performance
Heated Attic Roof Structure 1: Roof tiles, battens (3 cm), counter-battens (3 cm), vapor-permeable roof membrane, 15 cm of glass wool insulation between rafters, vapor barrier foil, 5 cm of glass wool insulation between the batten frame, OSB board (2 cm), plasterboard (1 cm), finished with plaster and paint. The structure's U-value = 0.151 W/m²K, which meets the regulation.
Unheated Attic Floor Ceiling Structure 1: Metal roof covering, vapor barrier bituminous membrane, OSB board (2 cm), rafter (10/15 cm), unheated attic space, overlaid glass wool insulation (10 cm), air gap (3 cm), glass wool insulation (5 cm), lower metal cladding with batten frame and air gap (2 cm), OSB board (2 cm), plasterboard (1 cm), finished with plaster and paint. The structure's U-value = 0.134 W/m²K, which meets the regulation.
9./ Summary
The ÉTDR is an administrative system where building permit and notification documentation must be managed. The TNM regulation defines the energy performance requirements for buildings, which must be verified in the design phase and supported by an energy certificate before occupancy.
Developers need to be well-informed about the legal framework, the design and permitting process, and keep an eye on the cost-value ratio of building materials. A well-informed builder or investor should choose a structural design that meets the requirements to save significant amounts, if that is a priority. However, if they opt for a long-term approach and choose over-designed structural layers to reduce future building maintenance costs, this must also be managed accordingly. Over-insulated or overly sealed structures might result in internal condensation, requiring mechanical ventilation systems, which involve additional costs. Not much has been said here about the internal moisture escape, which would require a separate device to control or eliminate. Therefore, the key is informed attention, adequate knowledge, and involving professionals in the design topics.
Images: Self-edited structural images with heat loss curves and values derived from the calculator.
Sources: